FOR IMMEDIATE RELEASE
NHERI Lehigh Experimental Facility Expands Capabilities for Cyber-Physical Testing
NSF-funded laboratory now offers dedicated shake table and testbeds for researchers in wind, earthquake and geotechnical engineering fields
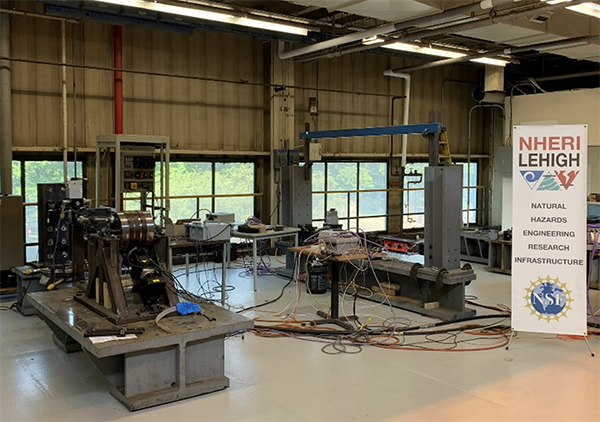
Two of 5 test beds at the NHERI Lehigh Real-time Cyber-Physical Structural Systems testing laboratory. (Image: NHERI Lehigh)
BETHLEHEM, PA, Sept. 24, 2021 In September 2021, the NHERI Lehigh University Experimental Facility unveiled expanded lab space and new equipment for conducting cyber-physical experiments. The enlarged facility opens the door wide for natural hazards researchers to explore structural mitigation solutions for windstorms and earthquakes.
Part of the NSF-funded Natural Hazards Engineering Research Infrastructure, the NHERI Lehigh Experimental Facility specializes in cyber-physical testing, a broad term that encompasses hybrid simulation, including real-time, multi-directional hybrid simulation experiments.
More space, more research opportunities
The new Real-time Cyber-Physical Structural Systems testing laboratory, RCPSS, consists of 2,000 additional square feet of of lab space, new testbeds, and a multi-directional shake table dedicated to cyber-physical testing.
Cyber-physical tests are ideal for large-scale structures that are impractical or impossible to test in a normal laboratory. Now, the expanded NHERI Lehigh Experimental Facility can accommodate more users and a broader range of hybrid testing applications.
The NHERI Lehigh RCPSS features five test beds, each with a dedicated dynamic actuator that can be linked to a multi-directional shake table.
These dedicated test beds exist independently from, but parallel to, our current laboratory setup, said Jim Ricles, principal investigator and director of the NHERI Lehigh Experimental Facility. We can now support additional concurrent users in the NHERI Lehigh Experimental Facility, and we can easily link these new testbeds with our existing setup.
Multi-directional shake table
A real-time integrated control system links the test beds to the multi-directional shake table. This allows users to conduct concurrent tests that are synchronized in real-time by simultaneously engaging the various test beds and the shake table. With efficiency and accuracy, researchers can test multiple structural designs, and multiple design solutions, at once.
We constructed our shake table in response to user requests, and it has significantly expanded the types of experiments we can run, said Ricles. For example, as it moves in the horizontal directions along an X-Y axis, the shake table can mimic the twisting, torsional effects of a structures floor under windstorm or earthquake loading.
Specifications and use-case scenarios for the RCPSS shake table, testbeds and computational controls are available on the NHERI Lehigh Experimental Facilitys website.
Plots of shake table tests show (left) measured force-deformation of a floor isolation system specimen in the two directions, and (right) the corresponding displacement orbits in the two directions. (Image: NHERI Lehigh. Data: RII Track-4: Quantifying Seismic Resilience of Multi-Functional Floor Isolation Systems through Cyber-Physical Testing (OIA 1929151), PI - Scott Harvey, University of Oklahoma.)
Pioneering hybrid experimentation
For more than a decade, the team at NHERIs Lehigh Experimental Facility has trained and supported natural hazards researchers in cyber-physical testing.
"Our facility is unique in the nation. We are one of the few labs in the U.S. dedicated to supporting large-scale, real-time, 3D cyber-physical testing, and we now provide a greater variety of options for researchers, said Ricles. For instance, our new multidirectional shake table can realistically emulate twisting motions that structures sometimes demonstrate under extreme 3-D wind loading due to non-uniform wind pressures acting over the façade of the building along with possible vortex shedding. Further, our new shake table can be deployed in quasi-static testing as well as hybrid simulation experiments.
Researchers rely on the NHERI Lehigh Experimental Facility to help them design hybrid simulation experiments that combine computer simulations of large structures with physical protective devices. By combining the number-crunching power and accuracy of computer simulations with the physical muscle of hazard mitigation devices, researchers can discover the best ways to protect our civil infrastructure structures such as industrial and manufacturing facilities, power transmission towers and skyscrapers from the effects of earthquakes and windstorms.
The real-time integrated control system includes tools for creating complex nonlinear computational models (both with material and geometric nonlinearities) that can be used for numerical simulation or real-time hybrid simulation. Users of the RCPSS can readily perform 3-D real-time hybrid simulations consisting of multiple experimental substructures and nonlinear analytical substructures.
An example real-time hybrid simulation might consist of multiple experimental substructures comprised of structural-response modification devices, devices such as passive or semi-active controlled dampers, tuned mass dampers, or isolation systems. The devices can be placed in the test beds and on the shake table. Then, these experimental substructures, i.e., the physical assemblies, are linked to the analytical substructure, a computational model of the remaining parts of the system, to define the complete system subjected a natural hazard such as an earthquake or wind storm.
Tools are available to include the effects of soil-foundation-structural system interaction in experiments by modeling the soil and foundation numerically as part of an analytical substructure, or by creating another experimental substructure using the facilitys soil boxes.
The RCPSS shake table with multi-directional translation and torsional in-plane motion applied. Note the roller bearing system. (Image: NHERI Lehigh)
The NHERI Lehigh team is available to help users understand and design cyber-physical testing programs. (Image: NHERI Lehigh)
Spotlight: Research Projects Using the NHERI Lehigh RCPSS Lab
The RCPSS lab supports a variety of research protocols, as demonstrated by the new laboratorys first experimental programs.
- Professor Scott Harvey of the University of Oklahoma is using the RCPSS for his project that investigates the dynamics of floor isolation systems, Quantifying Seismic Resilience of Multi-Functional Floor Isolation Systems through Cyber-Physical Testing.
University of Oklahoma graduate researcher assistant Esteban Villalobos Vega deploys NHERI Lehighs RCPSS shake table for a study of floor isolation systems. (Image: NHERI Lehigh)
- Professor Nicos Makris of Southern Methodist University is using NHERI Lehighs new lab for his work developing a novel damping device, a pressurized sand damper, including its performance at elevated and cold temperatures, in a project called Investigation of a Novel Pressurized Sand Damper for Sustainable Seismic and Wind Protection of Buildings.
- Professor Claudia Marin of Howard University plans to use the RCPSS resources and its computational modeling tools for research on structural condition assessment and motions using photographic imagery pattern recognition and machine learning. The project is NSF Convergence Accelerator Track D: Intelligent Surveillance Platform for Damage Detection and Localization of Civil Infrastructure.
- Professor Carla Lopez of the University of Puerto Rico Mayaguez and Professor Humberto Cavallin of the University of Puerto Rico-Rio Piedras will use the RCPSS and the NHERI Lehigh testing and computational tools to study resilient infrastructure subjected to natural hazards and to promote sustainability education. The projects are Building Capacity: A Collaborative Undergraduate STEM Program in Resilient and Sustainable Infrastructure (Award #1832468) and Building Capacity: A Collaborative Undergraduate STEM Program in Resilient and Sustainable Infrastructure (Award #1832427.
Benefits of cyber-physical testing
Traditionally, cyber-physical testing has been used to explore performance in large-scale structures. But the hybrid method is valuable for a wide range of experimental programs. Inexpensively and efficiently, hybrid testing can help researchers define and fine-tune the design of hazard mitigation measures. By enabling early investigations to hone in on specific technical challenges, hybrid tests can help researchers advance their investigations faster and with greater accuracy. For example, the RCPSS is available for users to perform pilot studies for generating data to include in their NSF-sponsored research proposals.
Fall training workshops. The staff at the NHERI Lehigh Experimental Facility encourage users of all experience levels to explore the RCPSS. On-site training workshops, which begin at the NHERI Lehigh Experimental Facility this fall, will enable participants to discover how cyber-physical testing can benefit their particular field of investigation. The workshops will demonstrate how hybrid simulation tests work as both real-time simulations and as quasi-static simulations. Participants will perform hands-on exercises that use the RCPSS test beds, shake table, and 3-D nonlinear modeling resources.
As specialists in cyber-physical testing, the NHERI Lehigh Experimental Facility team is dedicated to educating researchers about ways hybrid experimentation can enhance research programs in natural hazards engineering. The group encourages inquiries from researchers curious about ways cyber-physical testing can advance their work. Please contact NHERI Lehigh research engineer Dr. Liang Cao or facility director Professor James Ricles.
Find details about cyber-physical testing, including the new Real-time Cyber Physical Structural Systems lab, on the NHERI Lehigh Experimental Facility website.
Media Contacts
James M. Ricles, PhD, PE
NHERI Lehigh EF PI
Bruce G. Johnston Professor of Structural Engineering
Director, Real-Time Multi-directional Earthquake Simulation Facility
Deputy Director, ATLSS Engineering Research Center
Phone: 610-758-6252
jmr5@lehigh.edu
About the Natural Hazards Engineering Research Infrastructure
Funded by the National Science Foundation, the Natural Hazards Engineering Research Infrastructure, NHERI, is a network of experimental facilities dedicated to reducing damage and loss-of-life due to natural hazards such as earthquakes, landslides, windstorms, and tsunamis and storm surge. It is supported by the DesignSafe Cyberinfrastructure. NHERI provides the natural hazards engineering and social science communities with the state-of-the-art resources needed to meet the research challenges of the 21st century. NHERI is supported by multiple awards from NSF, including the NHERI Network Coordination Office, Award #2129792 and NHERI NHERI Lehigh Experimental Faiclity, Award #2037771.